Study and Analysis of a Root Cause of Failure
in Resin Composite Materials
Evaluation of Residual Stress in Molded Resin
Evaluation of the Residual Stress in Resin-Molded Parts - Importance and Outline -
- In injection molding of resins the residual stress remains in the molded parts. While the external mechanical force applied to the molded part can be measured, the residual stress in
the molded parts is difficult to predict. Since the residual stress affects the performance and the durability of the molded parts, it is important to know the residual stress in the
molded parts.
Measurement of the residual stress allows for finding the way to reduce it, thus contributing to improve the quality of the molded products. - In the solvent immersion method the molded part is immersed in a particular solvent to cause cracking of the molded part with a certain level of residual stress and the stress levels in molded parts is quantified from the severity of cracking.
- In the 1/4 elliptical method the injection molded plate is strapped to the elliptical surface rig to generate the strain and the chemical is applied to the surface of the plate to reduce the intermolecular force in the molded parts to generate cracks. This method can determine the critical strain at which cracking occurs. This method is also good to know the level of effects by different chemicals.
Cause of Environmental Stress Cracking in the Molded Parts and Necessity of Testing
- Injection molded parts are produced by filling a die with molten resins under high pressure followed by cooling to solidify. Difference of the pressure applied to the parts, difference in the mold shrinkage rate, and difference in molecular orientation of the molten resin in die generate the residual stress such as tensile stress or compression stress.
- Exposure of injection molded parts with residual strain to a certain environmental substances (particularly organic solvents) reduces the intermolecular force of the resin to
generate and propagate cracks and crazes*1for releasing the residual stress, thereby resulting in failure of molded parts. This clearly indicates
importance to identify and quantify the cause and the severity of cracking.
*1) This is a deformation yield behavior inherent in polymer material, and may be a precursor for cracks in deformation and yield of molded parts.
JFE-TEC Can Perform the Environmental Stress Cracking test on the Molded Plate by the Bent Strip Method According to ASTM D1693.
- The bent strip method described in ASTM D1693 will be described below as the environmental stress cracking test method for the molded plate.
- The test specimens are notched for deeper penetration of the applied chemicals (external environmental substances).
- The test specimens are bent with the notch pointing upwards in a metal U-shaped specimen holder to generate excess residual stress.
- The test specimens under excess stress are immersed in the chemical (external environmental substances) to determine the time when the small cracks appear in the specimens.
Test Condition
-
(1)Dimension of the specimen
Test temperature Test piece thickness, C (mm) C mm Notch depth, D (mm) mm 50℃ 1.84-1.97 0.30-0.40 3.00-3.30 0.50-0.65 100℃ 1.84-1.97 0.30-0.40 -
(2)Dimension of the holder
-
(3)setting the specimen
Appearance of Test Piece
-
The test specimens are notched.
-
The test specimens are bent.
-
Cracks are observed after immersing in the chemicals.
Determination of the residual stress in the molded parts can be used for improvement of the product quality
Evaluation example by the method of immersion in chemicals
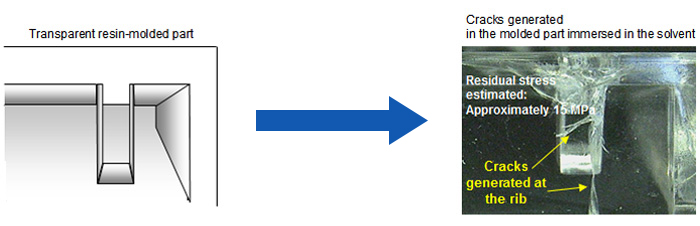
Test condition
- Materials: Polycarbonate.
- Solvent: Methyl isobutyl ketone (MIBK)/methanol
- Time: 1 min
Critical strain measurement by 1/4 ellipsoidal method
-
-
The surface of the test specimen is inspected to determine the severity of cracking (critical strain) from the location of cracks on the specimen.
Rough indication of the severity of cracks
Critical strain Less than 0.3% Application of slight stress is likely to initiate cracks 0.3-0.7% Contact with the chemical is likely to generate whitening and cracks. More than 0.7% Possibly of cracks is less even when contact occurs with the chemical.