Battery and Capacitor Prototyping
Battery Prototyping and Coated Material Preparation/Evaluation of Capacitors
JFE-TEC provides specific processing for coating solution preparation, coating itself and press forming of lithium-ion batteries (LIB), electric double layer capacitors (EDLC) and lithium-ion capacitors (LIC), and also performs evaluation of coating materials.
In order to improve performances of lithium-ion batteries (LIB), electric double layer capacitors (EDLC) and lithium-ion capacitors (LIC), micronization of electrode active materials and conductive auxiliary agents, reduction of binder addition, etc. have been promoted. Such changes in electrode materials and component ratios may affect dispersiveness and coating performance of electrode slurry (coating solution).
JFE-TEC provides assistance to client's problem solving on coating materials by offering the following evaluation services along with coating material preparation.
- Measurement of viscoelasticity of coating solution (slurry)
- Dispersiveness evaluation (sectional structure analysis ) of active materials, auxiliary agents and binder in coating film
- Chemical component analysis of coating film
JFE-TEC offers use of thin-film rotating type agitation device (thin-film rotating type high speed mixer) to agitate active materials, conductive auxiliary agents and binder used in prototyping processes (electrode coating preparation processes) for the study of dispersiveness of electrode slurry (coating solution) as well.
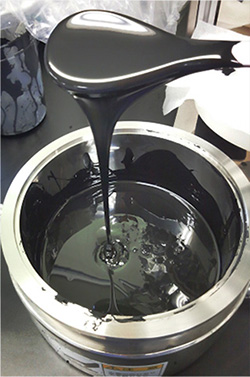
Measurement of viscoelasticity of coating solution (slurry)
JFE-TEC provides viscoelasticity measurement services using rheometer which uses small amount of sample to evaluate dispersiveness and coating capability of battery materials in electrode slurry of lithium-ion batteries (LIB), electric double layer capacitors (EDLC) and lithium-ion capacitors (LIC).
-
Rheometer (made by Brookfield) -
[Outline of specification]
- Measurement mode: stress control/rotation speed control
- Sample: 5 ml or less
- Torque range: 0.05-50 mNm
- Rotation speed range: 0.1-1000 rpm
- Measurement viscosity range: 0.02-3,200 Pa-s
1) Measurement of flow curve (rotation speed control)
Viscosity is measured by changing shear rate.
It is believed that the smaller effect of shear rate is (the smaller viscosity change is), the less failure due to speed variation in coating process occurs.
2) Measurement of hysteresis loop (rotation speed control) (Fig. 1)
Measurement is performed by continuously decreasing shear rate after continuous increase.
Area surrounded by shear rate vs shear stress curves corresponds to the quantity of structures broken by stress. It can be said that the larger the area becomes, the stronger _internal structure capability¤ is.
3) Measurement of yield point (stress control) (Fig. 2)
Study of inflection point of strain curve by continuously increasing stress loading in the sample. Stress required to break internal structure and initiate flow (yield point) can be evaluated.
When particle density is high like electrode slurry of lithium-ion secondary batteries, three dimensional network structure is formed under stationary conditions.
Force required to break the structure and initiate flow corresponds to the yield value.
In general, the higher dispersiveness of slurry is, the less structure formed and the smaller yield value becomes.
4) Measurement of creep recovery (stress control)
Elasticity and viscosity can be evaluated by the change of strain after applying a given stress to the sample.
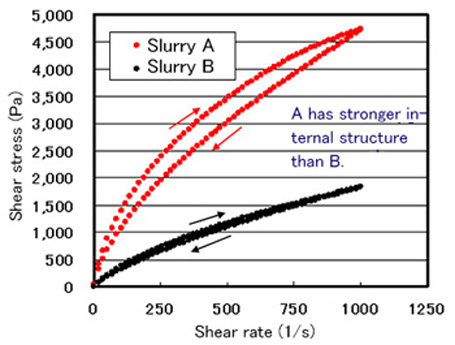
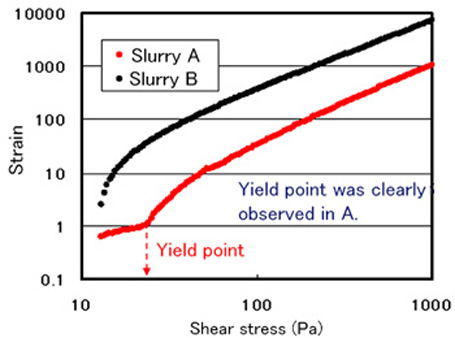
Dispersiveness evaluation example of coating solution (slurry)
Dispersiveness of battery materials in electrode slurry of lithium-ion batteries (LIB), electric double layer capacitors (EDLC) and lithium-ion capacitors (LIC) can also be evaluated by the comparison of SEM observation images and degree of capacity deterioration due to agitation cycle.
(Dispersiveness of added material are different due to the difference of agitation method in prototyping processes (electrode coating preparation processes).)
-
Planetary type agitation tank -
Thin-film rotating type high speed mixer
-
Example showing dispersiveness of particulate by SEM observation
Cross sectional SEM images of LCO positive electrode film (CNT addition) Superior dispersiveness in thin-film rotating type compare to planetary-type mixers
-
Example showing effect of dispersiveness to battery characteristics
Example of cycle characteristics evaluation (1C) Agitation time: 30 s, peripheral speed 20 m/s
Degree of cycle deterioration is low in thin-film rotating type compare to that in planetary-type.
(It can be presumed that it reflects dispersive conditions of CNT in film.)