Thermography (Infrared Camera Application Technology)
High Performance Thermal Measurement and Stress Measurement with Thermography (Infrared Camera) Explanation (2)
In-page menu
Defect Detection Technology
A method detecting failures or defects by measuring the thermal distribution in devices or buildings using an infrared camera has been the conventional method on maintenance sites. Use of the infrared camera in nuclear power and buildings is within this category. Although it is common to apply the passive method where the measurement object is not heated and measured as is, here, the active method that clarifies defects by heating the object is explained. The following methods have been put to practical use: (1) The heating method generates temperature differences at the defect point from heating for a certain period of time with a halogen lamp heater or a voltage load. Defects in the materials are identified from the difference in time that temperature waves pass through the object after cyclical heating. (Fig. 9) (2) The excitation method, on the other hand, identifies crack defects by heating the object using ultrasonic vibration or applying a voltage load to produce a thermal-elastic effect.
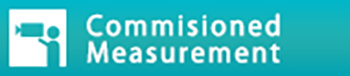
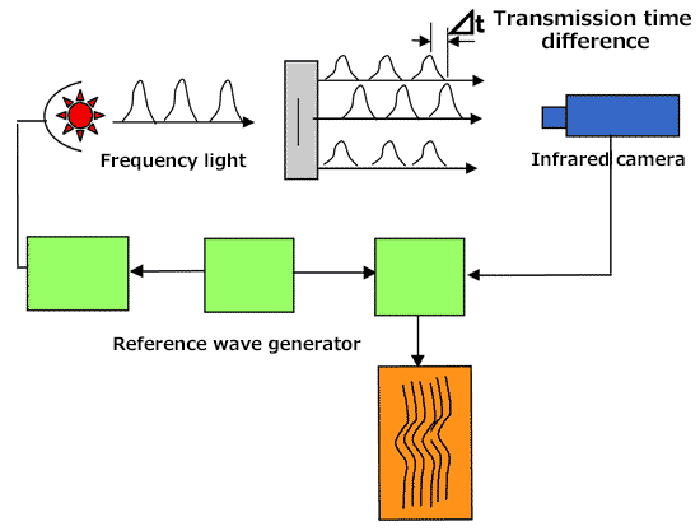
Fig. 10 shows an example where plate thickness of a member has become uneven due to plastic working and is thus measured with the cyclic heating method. This method is also used for measuring changes in physical properties of ion exchange membrane of battery or the distribution of carbon fibers or glass fibers in resin. For inspection of solar panels, this method is used to find defects using heat or light emission from cyclic energization, as well as analyzing the power generation efficiency and defects. Fig. 11 shows a method for finding defects in the sintered portion with ultrasonic vibrations. This method is also used for quality determination of mating portions and rivets.
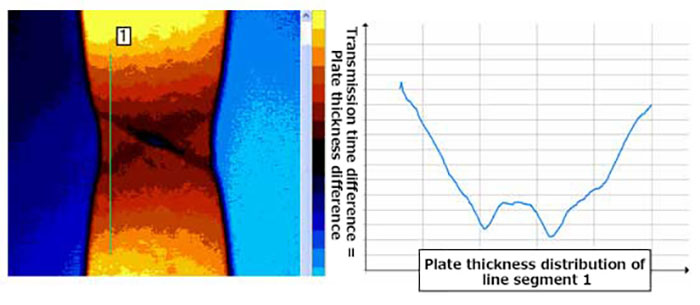
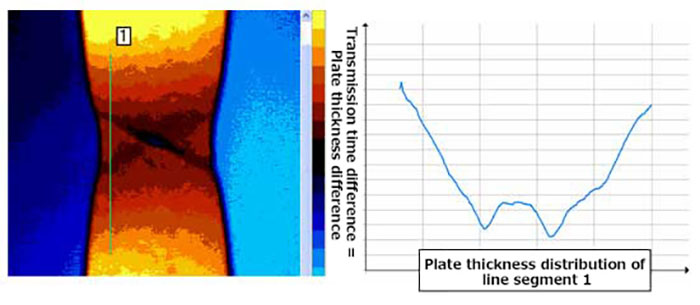
Conclusion
Uses of infrared cameras are expanding with the advances in hardware. However, unavailability of the high performance element is unfortunately a bottleneck because it was developed for military use, is produced overseas, and is very expensive.
Mid-class cameras with similar elements are available, and the infrared camera is becoming more familiar. Furthermore, the performance of general-purpose cameras has improved, even though there are differences from the high-performance camera; however, the general-purpose camera may cover many applications if customized software is developed in future.
Infrared cameras are expected to be used effectively in more fields.
Last of all, we would like to express our sincere thanks to Mr. Okazaki Yoshimitsu of the high-performance biomaterials group, Human Welfare Biomedical Research Division of the National Institute of Advanced Industrial Science and Technology, for his advice on stress measurement of bone implants.